Glass bead for blasting | Glass Bead Blasting Media
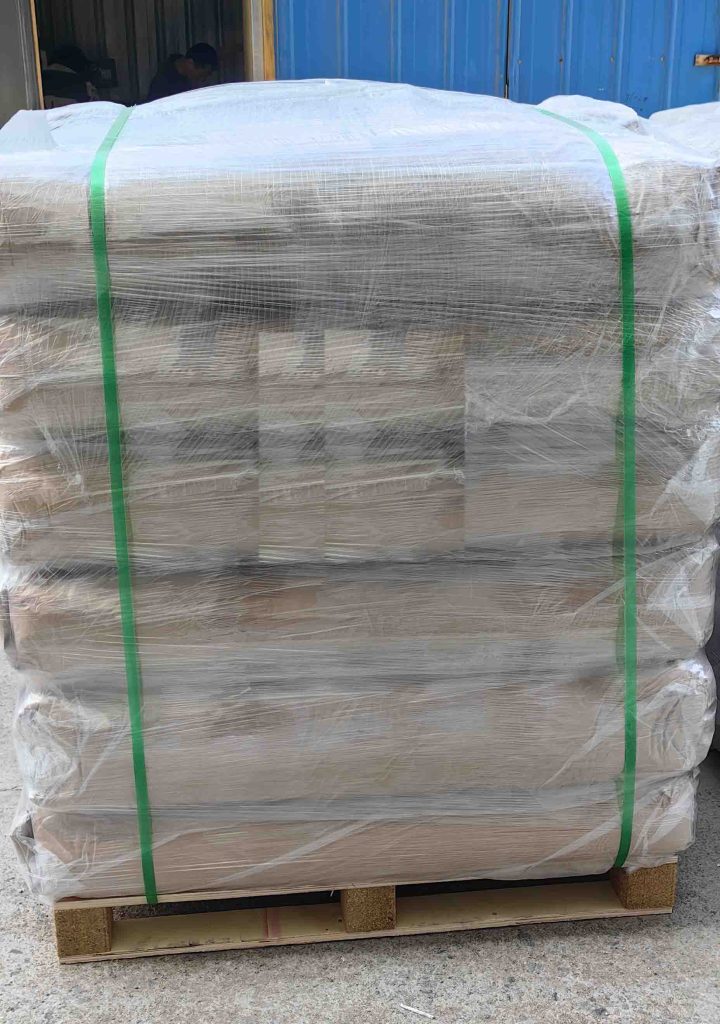
Glass bead for blasting
Glass beads are a common abrasive blasting medium, typically used for stainless steel, aluminum, or other non-ferrous metal parts to achieve a decorative surface effect.
Glass bead for blasting also assist in pre-treatment processes like nickel or chrome plating before galvanization, giving the substrate a clean, bright, matte finish.
What Are glass bead for blasting’s Applications?
Aerospace industry | Remove rust and paint from mechanical components to remove knife marks. |
Remove scratches on the rubber | Reflective paint for roads |
Scratch treatment on the surface of stainless steel. | |
Foundry industry; | Pre processing in the electroplating industry. |
Semiconductor Industry | Crafts for exterior decoration |
Glass bead for blasting | glass bead blasting media
In addition to treating newly manufactured parts, glass bead for blasting can be used to process old motor components or to polish artworks, decorations, and interior accessories.
They are effective in removing heavy coatings, paint, or rust from the surfaces of old parts, revealing a clean and tidy surface, and giving them a visually appealing shine similar to new parts.
To achieve the best results with glass bead for blasting, two main processing steps are generally required: blasting and polishing.
Firstly, let’s discuss the blasting stage. As a pre-treatment step before coating parts, glass beads can replace traditional abrasives like alumina or garnet, which are sharp and commonly used in the industry.
Glass bead for blasting help clean rust, scale, or mold residues from the material’s surface, creating a uniform appearance and avoiding inconsistent colors after heat treatment. Unlike traditional abrasives with sharp edges, glass beads for blasting prevent new scratches or other contaminants on the blasted parts, making them ready for further polishing. Polishing is the next step to give parts a beautiful satin finish.
In the industry, glass beads for blasting are often used for polishing because their spherical structure can smooth out sharp edges. After grinding, the high-hardness glass beads not only round off the part’s sharp features but also provide a soft satin finish, achieving a specific visual effect.
Additionally, glass beads for bead blasting can enhance the corrosion resistance and mechanical performance of the parts, reducing the risk of damage or defects after welding, grinding, or electric welding.
For producers, glass beads are a cost-effective abrasive blasting and polishing material. Besides the processing characteristics mentioned above, glass beads offer the following advantages:
• The chemical stability of glass beads ensures they do not easily react with other chemicals. In actual production, glass beads can be flexibly mixed with other materials, ensuring both safety and reliability.
• Glass beads can process sensitive surfaces or serve in precise cleaning scenarios without significantly altering the part’s shape. They polish, decorate, deburr, and harden surfaces, making them a gentle abrasive medium.
• Glass beads are typically made from recycled glass and can be reused up to six times. We offer discount services for recycled processing upon customer request, and the secondary processing does not affect the performance of the glass beads. This not only reduces costs but also reflects the company’s commitment to environmental protection.
• Glass beads do not contain silica, which poses respiratory risks. Using glass beads instead of traditional abrasive materials can effectively protect the health of blasting operators. Choosing the appropriate size, color, and hardness of glass beads for different parts is crucial for the final appearance of the product.
Our glass beads are usually packaged in 25 kg bags, and we also offer customized services to meet special application needs. Please contact customer service for more details.
Size of glass beads for blasting
Model of Bead blasting glass | Sieve Size (mesh) | Particle Size Range(μm) |
WSL17L# | 20~40 | 425 ~ 850 |
WSL 18L# | 30~40 | 425 ~ 600 |
WSL 19L# | 40~60 | 300 ~ 425 |
WSL 20L# | 60~100 | 150 ~ 300 |
WSL 21L# | 70~140 | 106 ~ 212 |
WSL 22L# | 100~140 | 106 ~ 150 |
WSL 23L# | 100~200 | 75 ~ 150 |
WSL 24L# | 140~200 | 75 ~ 106 |
WSL 25L# | 140~270 | 53 ~ 106 |
WSL 26L# | 200~325 | 45 ~ 75 |
Specification of Bead blasting glass
Specific gravity | 2.4-2.6 g/m3 |
Stacking density | 1.5g/cm3 |
Type | Blasting / Shot Peening Media |
Spherical | |
Rockwell hardness: | 46HRC |
Mohs | 6-7 |
Round rate | 80% |
Melting point | 710-730 ℃ |
Index of refraction | 1.5—1.6 |
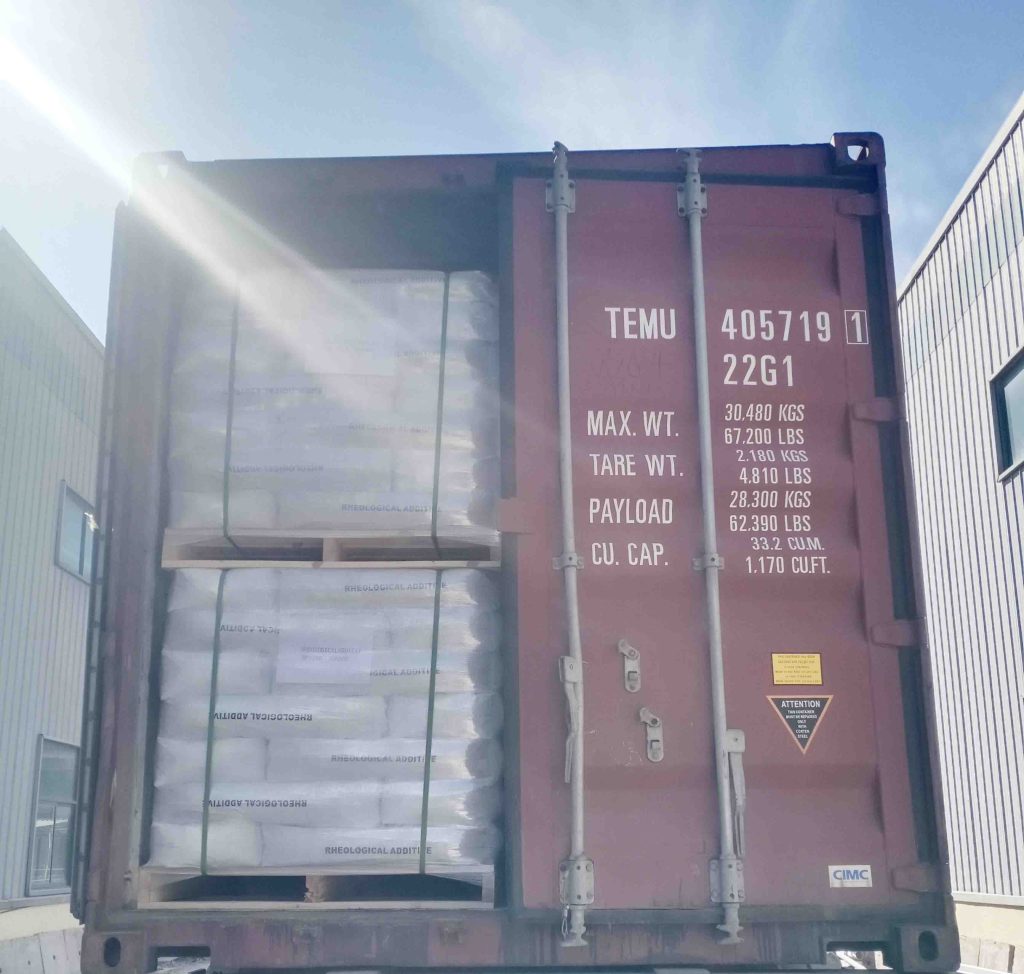
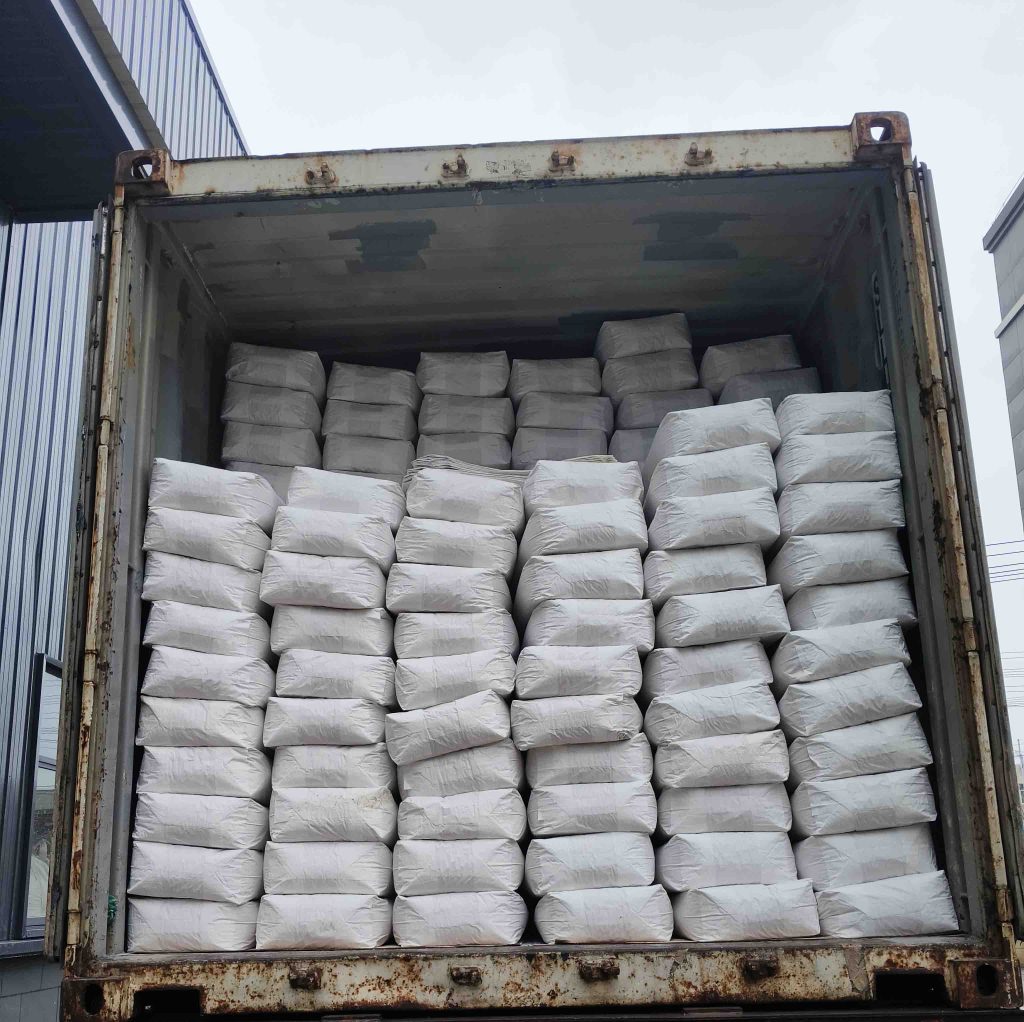
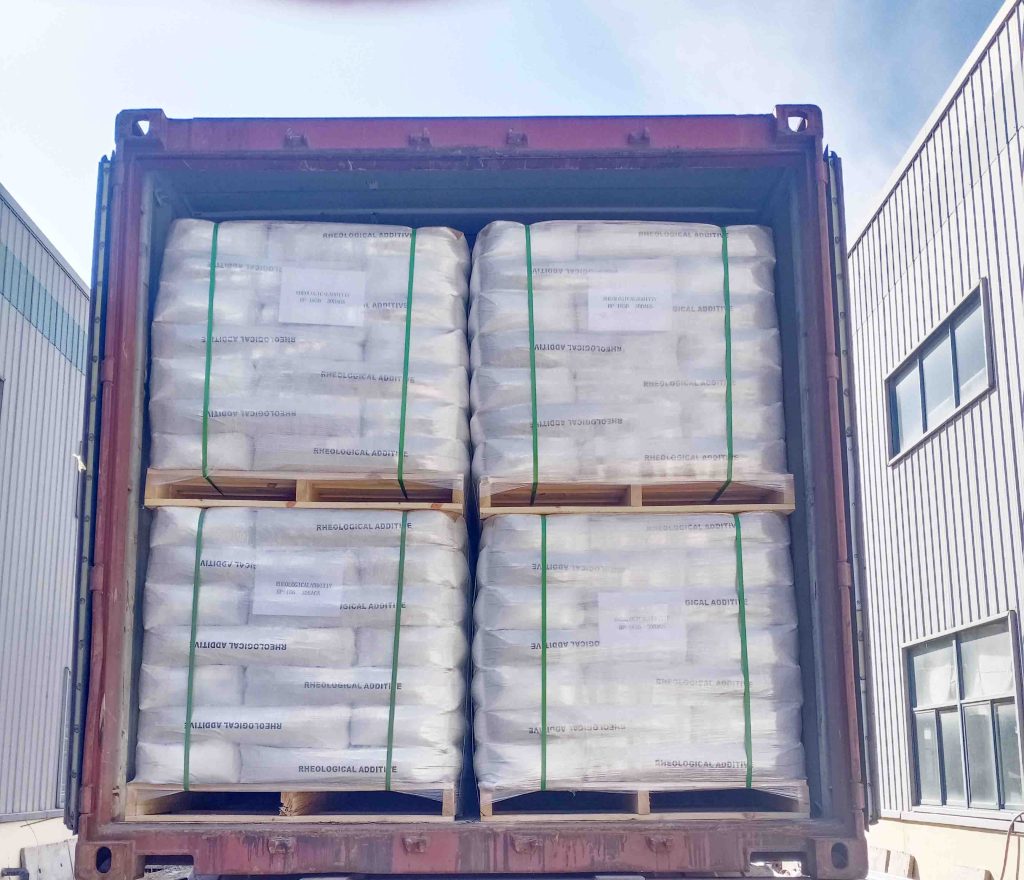