Organobentonite: Advanced Rheological Additive for Industrial Applications
In today’s competitive industrial landscape, manufacturers are constantly seeking innovative materials that can enhance product performance while meeting stringent environmental standards.
Organobentonite stands out as a remarkable solution that has revolutionized multiple industries through its exceptional rheological properties and versatile applications.
This advanced material, created through the organic modification of natural bentonite clay, offers superior performance characteristics that make it indispensable in various industrial processes.
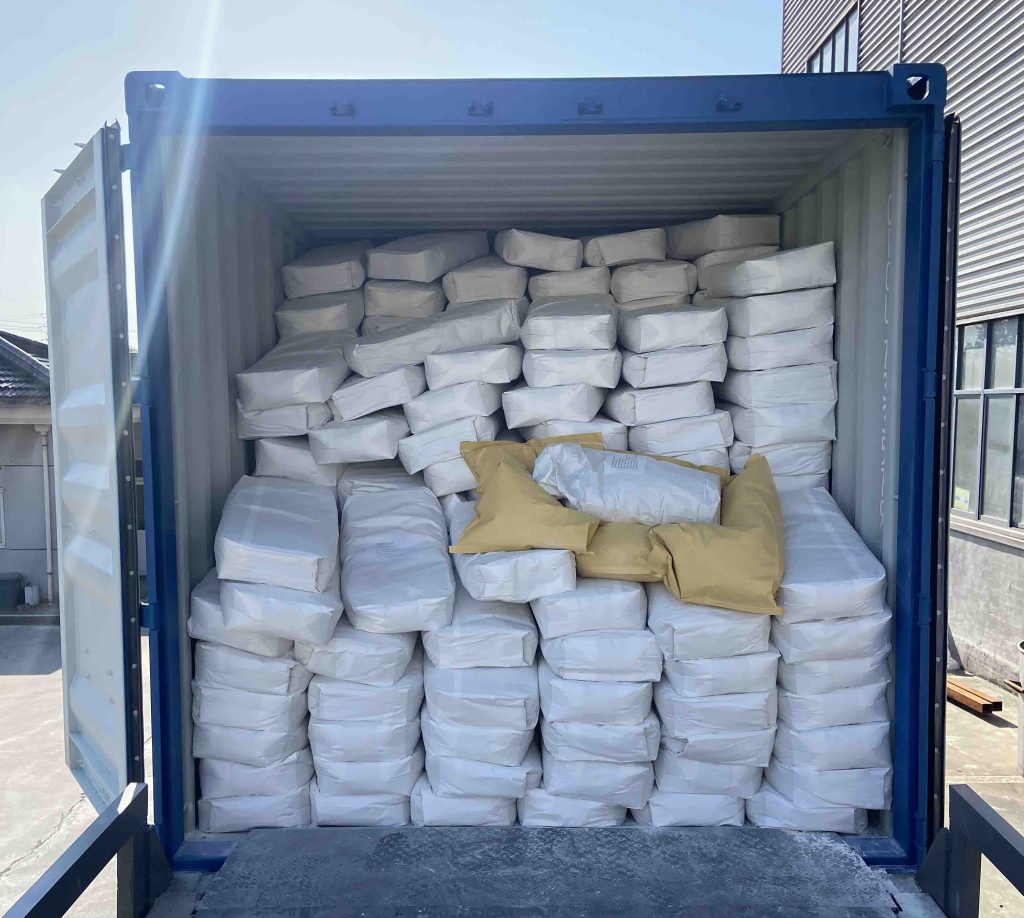
Whether you’re looking to improve the stability of your formulations, enhance the
efficiency of your production processes, or develop more environmentally friendly
products, understanding the capabilities and applications of organo bentonite is
essential. This comprehensive guide explores everything you need to know about this
versatile material, from its fundamental properties to its wide-ranging industrial
applications and future development trends.
What is Organobentonite?
Organo clay is an organically modified clay mineral derived from natural bentonite
through a process of surface modification with organic compounds. At its core,
organophilic clay is created by replacing the inorganic exchangeable cations (typically
Na+, Ca2+, or Mg2+) present in natural montmorillonite (the primary mineral
component of bentonite) with organic cations, most commonly quaternary ammonium
compounds or polymers.
The chemical structure of organobentonite consists of nanometer-thick aluminosilicate
layers with organic molecules intercalated between them. This unique structure
fundamentally transforms the properties of the original bentonite clay, converting it
from a hydrophilic (water-loving) material to an organophilic (organic-loving) one. The organic modification significantly alters the surface properties, expanding the interlayer spacing and creating a material with enhanced affinity for organic compounds.
Unlike conventional bentonite, which disperses readily in water but poorly in organic systems, organobentonite exhibits excellent dispersibility in organic media such as solvents, resins, and oils. This fundamental difference stems from the organicmodification process, which shields the hydrophilic silicate surfaces with hydrophobic
organic groups, effectively reversing the natural clay’s polarity.
The preparation of organoclays typically involves several key steps:
- Purification of raw bentonite to remove impurities and concentrate the
montmorillonite content
- Dispersion of the purified bentonite in water to create a stable suspension
- Addition of organic modifiers (quaternary ammonium salts, polymers, or other
organic compounds)
- Ion exchange reaction between the inorganic cations in the clay and the organic
cations
- Filtration, washing, and drying of the modified clay
- Grinding and classification to achieve the desired particle size distribution
The degree of organic modification and the specific organic compounds used can be tailored to meet the requirements of different applications, resulting in a wide range of organobentonite products with varying properties and performance characteristics.
Properties and Characteristics of Organobentonite
The unique combination of inorganic and organic components in organic bentonite clay results in a material with exceptional properties that make it highly valuable across multiple industries. Understanding these properties is crucial for selecting the right organic bentonite product for specific applications.
Physical Properties
Organobentonite typically appears as a fine, off-white to light tan powder with a specific
gravity ranging from 1.7 to 1.8. The particle size distribution can be controlled during
manufacturing, but typically ranges from 2 to 75 microns, with a median particle size of
approximately 6-8 microns. This fine particle size contributes to its high specific surface
area, which typically ranges from 300 to 800 m²/g, providing extensive surface area for
interactions with surrounding media.
One of the most significant physical changes resulting from organic modification is the
increase in the interlayer spacing of the clay. While natural montmorillonite has an
interlayer spacing of approximately 1.2-1.4 nm, organobentonite can exhibit expanded
spacings of 1.8-3.5 nm, depending on the size and arrangement of the intercalated
organic molecules. This expanded structure facilitates the interaction with organic
compounds and contributes to its rheological properties.Chemical Properties
The cation exchange capacity (CEC) of rheological additive bentonite, typically ranging from 70 to 120
meq/100g, indicates its ability to exchange cations and is a measure of the degree of
potential organic modification. The organic content, which can range from 20% to 40%
by weight, reflects the amount of organic modifier incorporated into the clay structure.
The surface chemistry of organobentonite is dominated by the organic groups
introduced during modification, which determine its compatibility with different media.
Depending on the specific organic modifier used, the surface can exhibit varying degrees
of hydrophobicity and organophilicity, allowing for customization to suit different
application requirements.
Rheological Properties
Perhaps the most valuable characteristic of organobentonite is its exceptional
rheological properties. When properly dispersed in compatible systems,
rheology modifiers forms a three-dimensional network structure that imparts thixotropic properties to the system. This means that the material exhibits high viscosity under
static conditions but flows more readily when subjected to shear forces—a property that is particularly valuable in coatings, greases, and other industrial formulations.
The thickening effect of organoclays is concentration-dependent and can be
precisely controlled by adjusting the dosage. Typically, concentrations of 0.5% to 5% by weight are sufficient to achieve significant rheological modification in most systems.
The thickening mechanism involves the formation of a “house of cards” structure, where the edges of the clay platelets interact with each other through the organic modifiers,
creating a network that restricts flow.
Adsorption Properties
The organic modification of bentonite significantly enhances its adsorption capabilities for organic compounds. The hydrophobic nature of the modified surfaces makes organobentonite an excellent adsorbent for oils, solvents, and various organic pollutants.
Adsorption capacities can range from 50 to 300 mg/g, depending on the specific rheology modifier and the target compound.
This adsorption capability is particularly valuable in environmental applications, where rheological additive can be used to remove organic contaminants from water and soil. The mechanism involves both surface adsorption and partition of organic compounds into the organic phase of the modified clay.Thermal and Environmental Stability
Organic clay exhibits good thermal stability, typically maintaining its structural
integrity and performance characteristics at temperatures up to 200-250°C, depending
on the specific organic modifier used. This thermal stability makes it suitable for
applications involving elevated processing or service temperatures.
In terms of environmental stability, organic bentonite is generally resistant to
degradation under normal environmental conditions. However, the organic components
may be susceptible to oxidation or biodegradation over extended periods, particularly in
harsh environments. The stability can be enhanced through the selection of more
resistant organic modifiers or through additional treatment processes.
Types of Organobentonite Products
The diversity of organobentonite products available in the market reflects the
versatility of this material and its ability to be tailored for specific applications.
Understanding the different types can help in selecting the most appropriate product for
particular industrial needs.
Classification by Organic Modifier
Quaternary Ammonium-Modified Organobentonites
These represent the most common type of organobentonites, produced by modifying
bentonite with quaternary ammonium compounds such as dimethyl dihydrogenated
tallow ammonium chloride (DMHT) or benzyl dimethyl hydrogenated tallow ammonium
chloride (BDMHT). The length of the alkyl chains in these compounds significantly
influences the properties of the resulting organobentonite, with longer chains typically
providing better compatibility with non-polar systems.
These products excel in organic media such as aliphatic and aromatic solvents, making
them ideal for oil-based drilling fluids, solvent-based coatings, and greases. They
typically require activation with polar additives like acetone, methanol, or propylene
carbonate to achieve optimal dispersion and performance.
Polymer-Modified Organobentonites
These advanced organophilic clays are produced by modifying bentonite with polymeric
compounds such as polyacrylic acid (PAA), polyethylene oxide (PEO), or various
copolymers. The polymer chains can intercalate between the clay layers or adsorb onto
the clay surfaces, creating a hybrid organic-inorganic material with unique properties.Polymer-modified organobentonites often exhibit enhanced thermal stability and
improved compatibility with polymer matrices, making them particularly valuable as
rheological additives in polymer composites and as binders in foundry applications. The
interaction between the polymer and the clay can also result in synergistic effects that
enhance the overall performance of the material.
Classification by Application Medium
Oil-Based Organobentonites
Specifically designed for compatibility with non-polar and moderately polar organic
media, these organobentonites are typically modified with quaternary ammonium
compounds having long alkyl chains. They excel in systems such as mineral oils,
vegetable oils, aromatic solvents, and various petroleum products.
Oil-based organobentonites are widely used as rheological additives in lubricating
greases, oil-based drilling fluids, solvent-based coatings, and printing inks. They provide
excellent thickening, anti-settling, and anti-sagging properties in these applications.
Water-Based Organobentonites
These specialized organobentonites are designed to maintain some degree of
hydrophilicity while incorporating organophilic properties. They are typically produced
using organic modifiers with hydrophilic groups or through partial modification of the
clay.
Water-based organobentonites find applications in water-based coatings, emulsions,
and certain environmental remediation processes. They can provide rheological control
in aqueous systems while also offering some compatibility with organic components in
mixed systems.
Classification by Performance Characteristics
High-Efficiency Organobentonites
These premium products are designed to deliver maximum rheological performance at
lower dosages. They typically undergo additional processing steps to enhance their
dispersion characteristics and rheological efficiency. High-efficiency organobentonites
may require less activation and provide superior performance in demanding
applications.Economy-Grade Organobentonites
These products offer a balance between performance and cost, making them suitable for
applications where extreme rheological control is not required. They typically require
standard activation procedures and may be used at slightly higher dosages to achieve
the desired effects.
Specialty Organobentonites
These include custom-formulated products designed for specific applications or to meet
particular performance requirements. Examples include organobentonites with
enhanced thermal stability for high-temperature applications, those with improved
chemical resistance for aggressive environments, or those with specific surface
treatments for enhanced compatibility with particular systems.
Industrial Applications of Organobentonite
The versatility of organobentonite has led to its adoption across a wide range of
industries, where its unique properties address specific challenges and enhance product
performance. The following sections explore the major application areas and the
specific benefits that organobentonite brings to each.
Coatings and Inks Industry
In the coatings and inks industry, organobentonite serves as a critical rheological
additive that provides multiple benefits to formulations. When properly dispersed in
solvent-based paints, varnishes, and lacquers, organobentonite creates a three
dimensional network structure that imparts thixotropic properties to the system. This
thixotropy prevents settling during storage, reduces sagging during application, and
improves leveling for a smoother finish.
For printing inks, particularly those used in gravure and flexographic printing,
organobentonite controls flow properties to ensure precise transfer of the ink to the
substrate. It prevents bleeding and feathering while maintaining color intensity and
print definition. The anti-settling properties also extend the shelf life of inks by
preventing pigment separation.
Typical dosage levels in coating applications range from 0.5% to 3% by weight,
depending on the specific formulation requirements and the type of organobentonite
used. For optimal performance, the organobentonite is typically pre-dispersed in a
suitable solvent with a polar activator before incorporation into the final formulation.Lubricants and Greases
In lubricating greases, organobentonite functions as a thickening agent that provides
structure and consistency to the formulation. Unlike conventional soap-based
thickeners, organobentonite-based greases offer superior thermal stability, water
resistance, and performance under high shear conditions.
The three-dimensional network formed by organobentonite in mineral or synthetic oils
creates a stable structure that holds the lubricant in place while allowing controlled
release during operation. This structure also provides excellent mechanical stability,
ensuring that the grease maintains its consistency even under severe mechanical
working.
Organobentonite-based greases are particularly valuable in high-temperature
applications, where they can maintain their structure and performance at temperatures
up to 200°C, significantly outperforming many conventional greases. They are widely
used in automotive, industrial, and marine applications where extreme conditions are
encountered.
Environmental Applications
The strong adsorption capabilities of organobentonite make it an effective material for
environmental remediation, particularly for the removal of organic contaminants from
water and soil. When used in wastewater treatment, organobentonite can efficiently
remove oils, greases, phenols, chlorinated compounds, and various other organic
pollutants through a combination of adsorption and partition mechanisms.
In soil remediation, organobentonite can be used as a barrier material to prevent the
migration of organic contaminants or as an amendment to immobilize pollutants in
contaminated soils. The hydrophobic nature of organobentonite allows it to
preferentially bind organic compounds, reducing their bioavailability and potential
environmental impact.
Recent research has also explored the use of organobentonite in the removal of
emerging contaminants such as pharmaceuticals, personal care products, and
endocrine-disrupting compounds from water. The high adsorption capacity and
selectivity for organic compounds make organobentonite a promising material for
addressing these challenging environmental issues.
Foundry Industry
In the foundry industry, organobentonite serves as both a binder and a lustrous carbon
carrier in bentonite-bonded molding sands. The organic modification of bentoniteenhances its binding properties while also providing a source of carbon that improves
the surface quality of castings.
When used in molding sands, organobentonite helps to reduce defects such as veining,
scabbing, and penetration by forming a protective barrier between the molten metal
and the sand mold. The organic components decompose during casting to form lustrous
carbon, which prevents metal penetration and improves the surface finish of the
castings.
The use of organobentonite in foundry applications also offers environmental benefits
by reducing emissions of volatile organic compounds (VOCs) and other harmful
substances during the casting process. This makes it an attractive alternative to
conventional carbon additives such as coal dust or petroleum-based products.
Other Emerging Applications
Beyond the established applications, organo bentonite is finding new uses in various
emerging fields:
- In polymer composites, organophilic clays bentonite serves as a nanofiller that enhances
mechanical properties, thermal stability, and barrier characteristics. The
intercalation or exfoliation of polymer chains between the clay layers creates
nanocomposites with significantly improved performance compared to
conventional filled polymers.
- In pharmaceutical and cosmetic formulations, organobentonite functions as a
rheology modifier, stabilizer, and delivery vehicle for active ingredients. Its ability
to form gels in organic media makes it valuable for controlling the consistency and
release properties of various personal care products.
- In oil and gas drilling, specialized organobentonites are used as rheological
additives in oil-based drilling fluids, providing viscosity control, suspension of drill
cuttings, and stability under high-temperature and high-pressure conditions.
- In adhesives and sealants, organoclays bentonite improves thixotropy, prevents sagging,
and enhances the mechanical properties of the cured products. It is particularly
valuable in formulations that must maintain their position after application but
before curing.
Advantages of Organobentonite in Industrial Processes
The incorporation of organobentonite into industrial formulations and processes offers
numerous advantages that contribute to improved product performance, enhancedprocess efficiency, and reduced environmental impact. Understanding these advantages
helps to appreciate the value proposition of clay in various applications.
Enhanced Product Performance
One of the primary advantages of rheological bentonite is its ability to significantly enhance
the performance characteristics of the products in which it is incorporated. In coatings
and inks,rheological additive improves application properties, prevents settling and
sagging, and enhances the overall appearance of the finished product. The thixotropic
properties it imparts allow for easier application while ensuring that the coating remains
in place on vertical surfaces.
In lubricating greases, organobentonite provides exceptional mechanical stability, high
temperature performance, and water resistance. Greases formulated with
organobentonite maintain their consistency under severe operating conditions,
extending the service life of lubricated components and reducing maintenance
requirements.
For environmental applications, the high adsorption capacity and selectivity of
organobentonite for organic compounds result in more efficient removal of
contaminants from water and soil. This leads to improved remediation outcomes and
better protection of environmental resources.
Process Efficiency and Simplification
The use of organobentonite can streamline manufacturing processes and improve
operational efficiency in several ways. Its effectiveness at low dosages means that less
material is required to achieve the desired rheological properties, reducing raw material
costs and simplifying inventory management.
The thixotropic behavior provided by organobentonite allows for easier processing
during manufacturing. For example, in coating production, the reduced viscosity under
shear makes mixing, pumping, and filling operations more efficient, while the increased
viscosity at rest prevents settling during storage.
In foundry applications, organobentonite can serve dual functions as both a binder and
a lustrous carbon carrier, eliminating the need for separate additives and simplifying the
molding sand formulation process. This multifunctionality reduces the number of
ingredients that need to be handled, stored, and controlled.Cost-Benefit Analysis
While organobentonite may have a higher unit cost compared to some conventional
additives, a comprehensive cost-benefit analysis often reveals significant economic
advantages. The higher efficiency of organobentonite means that lower dosages are
required to achieve the desired effects, potentially resulting in overall cost savings.
The improved performance and extended service life of products formulated with
organobentonite can also translate into economic benefits for end-users. For example,
lubricating greases with better high-temperature stability require less frequent
replacement, reducing maintenance costs and equipment downtime.
In environmental applications, the high adsorption capacity of organobentonite can
make remediation processes more cost-effective by reducing treatment time and
resource requirements. The ability to regenerate and reuse organobentonite in some
applications further enhances its economic value proposition.
Environmental Benefits
The environmental advantages of organobentonite extend beyond its direct applications
in environmental remediation. The efficiency of organobentonite at low dosages means
that less material is required, reducing resource consumption and waste generation.
In foundry applications, organobentonite-based binders can reduce emissions of volatile
organic compounds (VOCs) and other harmful substances during the casting process.
This contributes to improved air quality in the workplace and reduced environmental
impact of foundry operations.
The natural origin of the base bentonite clay, combined with the potential for using bio
based organic modifiers, positions organobentonite as a more sustainable alternative to
some synthetic rheological additives. Ongoing research into environmentally friendly
organic modifiers continues to enhance the sustainability profile of organobentonite
products.
Comparison with Alternative Products
When compared to alternative rheological additives and performance enhancers,
organobentonite often offers a superior balance of properties and benefits. Unlike many
synthetic thickeners, organobentonite provides true thixotropic behavior, with rapid
recovery after shearing and excellent long-term stability.
In comparison to fumed silica, another common rheological additive, organobentonite
typically requires lower dosages to achieve similar thickening effects and offers bettercontrol of sag and settling. It also generates less dust during handling, improving
workplace safety and reducing product losses.
For environmental applications, organobentonite offers advantages over activated
carbon in terms of cost and selectivity for organic contaminants. While activated carbon
has a higher surface area and broader adsorption spectrum, organobentonite’s affinity
for organic compounds makes it more efficient for targeted removal of specific
contaminants.
How to Select the Right Organobentonite for Your
Application
Choosing the most appropriate organobentonite product for a specific application
requires careful consideration of various factors, including the nature of the application
medium, the desired performance characteristics, and the processing conditions. The
following guidelines can help in making an informed selection.
Application Requirement Analysis
The first step in selecting an organobentonite product is to clearly define the
requirements of the application. This includes identifying:
- The nature of the medium (solvent-based, oil-based, water-based, or mixed
systems)
- The desired rheological profile (degree of thixotropy, yield value, viscosity range)
- The processing conditions (temperature, shear rates, pH)
- The end-use requirements (stability, appearance, performance criteria)
- Any regulatory or environmental constraints
A comprehensive understanding of these requirements provides the foundation for
selecting an organobentonite product that will deliver the desired performance.
Key Performance Parameters
Several key parameters should be considered when evaluating organobentonite
products:
- Compatibility with the application medium: Different organobentonites are
designed for specific types of media. For non-polar systems like mineral oils or
aliphatic solvents, highly organophilic grades are typically required. For more polar
systems, moderately modified grades may be more suitable.• Activation requirements: Some organobentonites require activation with polar
additives to achieve optimal dispersion and performance. The availability and
compatibility of these activators with the overall formulation should be
considered.
- Efficiency: The dosage required to achieve the desired rheological properties
varies among different organobentonite products. Higher-efficiency grades may
have a higher unit cost but require lower dosages, potentially resulting in overall
cost savings.
- Particle size and dispersion characteristics: Finer particle sizes generally provide
better dispersion and higher efficiency but may be more difficult to incorporate.
The ease of dispersion is particularly important in production environments with
limited high-shear mixing capabilities.
- Thermal and chemical stability: For applications involving high temperatures or
aggressive chemicals, the stability of the organobentonite under these conditions
is a critical consideration.
Compatibility Considerations
The compatibility of organobentonite with other components in the formulation is
essential for achieving optimal performance. Key compatibility considerations include:
- Interactions with surfactants and dispersants: Some surfactants and dispersants
can interfere with the network structure formed by organobentonite, reducing its
effectiveness. Compatibility testing is recommended when these components are
present.
- pH sensitivity: While organobentonites are generally less sensitive to pH than
unmodified bentonites, extreme pH conditions can still affect their performance.
The pH range of the application should be considered in the selection process.
- Solvent polarity: The effectiveness of organobentonite is influenced by the
polarity of the solvent system. Matching the organobentonite type to the solvent
polarity is crucial for optimal performance.
- Presence of competing adsorbates: In applications involving multiple organic
compounds, competitive adsorption can affect the performance of
organobentonite. Understanding these interactions is important, particularly in
environmental applications.Testing and Validation Methods
Before finalizing the selection of an organobentonite product, laboratory testing and
validation are essential to confirm its suitability for the specific application. Common
testing methods include:
- Rheological measurements: Viscosity profiles at different shear rates, yield value
determination, and thixotropy assessment provide insights into the rheological
behavior of the organobentonite in the application medium.
- Dispersion quality assessment: Microscopic examination or filtration tests can
evaluate the degree of dispersion achieved, which directly affects performance.
- Stability testing: Accelerated aging tests under relevant conditions (temperature,
light, humidity) help predict the long-term stability of formulations containing
organobentonite.
- Application-specific performance tests: These may include sag resistance for
coatings, water resistance for greases, or adsorption efficiency for environmental
applications.
- Pilot-scale trials: Before full-scale implementation, pilot trials under actual
production conditions are recommended to validate laboratory findings and
identify any scale-up issues.
Optimization Recommendations
To maximize the performance of organobentonite in your application, consider the
following optimization strategies:
- Pre-dispersion: Preparing a pre-gel of organobentonite in a portion of the solvent
with appropriate activators before incorporation into the final formulation often
improves dispersion and performance.
- Activation optimization: The type and amount of polar activator can significantly
influence the efficiency of organobentonite. Optimization of the activator system
can enhance performance while minimizing costs.
- Processing conditions: The temperature, mixing speed, and duration of the
dispersion process all affect the final performance. Optimization of these
parameters can improve efficiency and consistency.• Synergistic combinations: In some applications, combining organobentonite with
complementary rheological additives can provide enhanced performance and cost
effectiveness.
Best Practices for Organobentonite Handling and
Application
Proper handling and application of organobentonite are essential for achieving optimal
performance and maximizing the value of this versatile material. The following best
practices provide guidance for storage, dispersion, and application of organobentonite
products.
Storage and Handling Recommendations
To maintain the quality and performance of organobentonite products, proper storage
conditions are essential:
- Store in a cool, dry place away from direct sunlight and moisture. Exposure to
moisture can affect the organobentonite’s performance, particularly in solvent
based applications.
- Keep containers tightly sealed when not in use to prevent contamination and
moisture absorption. For bulk storage, ensure that silos or bins are properly sealed
and protected from the elements.
- Implement appropriate inventory management practices, using older stock first
(first-in, first-out) to minimize storage time. While organobentonite products are
generally stable, prolonged storage may affect their performance in some
applications.
- When handling organobentonite powder, use appropriate dust control measures
and personal protective equipment. Although organobentonite is not classified as
hazardous, dust inhalation should be avoided as a general precaution.
- Allow cold material to warm to room temperature before opening containers to
prevent condensation, which can affect the powder’s flowability and dispersion
characteristics.Dispersion and Activation Techniques
Achieving proper dispersion of organobentonite is crucial for its performance as a
rheological additive. The following techniques can help ensure optimal dispersion:
- For solvent-based systems, pre-wet the organobentonite with a polar activator
(such as propylene carbonate, methanol, or a mixture of water and low-molecular
weight alcohols) before adding it to the main solvent. The typical ratio is 30-60%
activator based on the weight of organobentonite.
- Allow sufficient time (typically 5-15 minutes) for the activator to interact with the
organobentonite before adding the mixture to the main solvent. This pre-activation
step significantly improves dispersion efficiency.
- Use high-shear mixing equipment such as high-speed dispersers, rotor-stator
mixers, or ball mills to achieve complete dispersion. The high shear forces help to
separate the clay platelets and develop the three-dimensional network structure.
- For maximum efficiency, add the pre-activated organobentonite to the solvent
before incorporating other components such as pigments, fillers, or resins. This
allows the organobentonite to fully develop its structure without interference.
- Monitor the dispersion process using visual inspection, fineness of grind
measurements, or rheological tests to ensure that complete dispersion has been
achieved. Incomplete dispersion can result in reduced efficiency and performance
issues.
Addition Methods and Proportioning
The method of adding organobentonite to formulations and the proportioning of
components can significantly impact performance:
- The pre-gel method, where organobentonite is first dispersed in a portion of the
solvent to form a concentrated gel before being incorporated into the final
formulation, often provides the best results. Typical pre-gel concentrations range
from 5% to 10% organobentonite by weight.
- For direct addition methods, introduce the organobentonite slowly into the vortex
created by a high-speed mixer to prevent clumping and ensure even distribution.
Avoid dumping large amounts at once, as this can lead to agglomeration and poor
dispersion.• The dosage of organobentonite should be carefully controlled based on the
specific application requirements. Starting with the manufacturer’s recommended
dosage and adjusting based on performance testing is a good approach.
- In formulations containing multiple additives, the order of addition can be critical.
Generally, organobentonite should be added and fully dispersed before
introducing components that might interfere with its dispersion, such as
surfactants or wetting agents.
- For applications requiring precise control of rheological properties, consider
implementing automated dosing systems to ensure consistency in the amount of
organobentonite added to each batch.
Common Issues and Solutions
Even with proper handling and application procedures, certain issues may arise when
working with organobentonite. Here are some common problems and their solutions:
- Poor dispersion: Manifested as visible particles, grittiness, or reduced efficiency.
Solutions include increasing shear during mixing, optimizing the activator system,
or switching to a more easily dispersible grade of organobentonite.
- Compatibility issues: Indicated by flocculation, separation, or loss of rheological
properties when combined with other formulation components. Solutions include
adjusting the order of addition, modifying the activator system, or selecting an
alternative organobentonite grade more compatible with the specific formulation.
- Insufficient thickening: When the organobentonite does not provide the desired
viscosity or thixotropy. Solutions include increasing the dosage, ensuring complete
dispersion, optimizing the activator system, or selecting a higher-efficiency grade.
- Excessive thickening: When the formulation becomes too viscous for processing
or application. Solutions include reducing the dosage, adjusting the activator level,
or selecting a lower-efficiency grade.
- Syneresis or bleeding: The separation of liquid from gels or greases containing
organobentonite. Solutions include adjusting the organobentonite-to-liquid ratio,
modifying the activator system, or incorporating complementary thickeners.Safety Handling Guidelines
While organobentonite products are generally considered safe for industrial use,
appropriate safety measures should be implemented:
- Review the Safety Data Sheet (SDS) for specific handling precautions and
emergency procedures related to the particular organobentonite product being
used.
- Use appropriate personal protective equipment, including dust masks or
respirators when handling dry powder, gloves to prevent skin contact, and eye
protection.
- Implement dust control measures in the workplace, such as local exhaust
ventilation, dust collection systems, or wet handling procedures where
appropriate.
- Provide training to personnel on proper handling procedures, including spill
response and disposal methods.
- Establish appropriate waste management procedures in accordance with local
regulations. While organobentonite is generally not classified as hazardous waste,
specific regulations may apply depending on the jurisdiction and the application.
Future Trends in Organobentonite Technology
The field of organobentonite technology continues to evolve, driven by advances in
materials science, growing environmental concerns, and expanding application
requirements. Understanding these trends provides insights into the future direction of
organobentonite development and applications.
Research and Development Directions
Current research in organobentonite technology focuses on several key areas:
- Novel organic modifiers: Researchers are exploring new types of organic
modifiers, including bio-based and renewable compounds, to enhance
performance while reducing environmental impact. These include modified plant
oils, biopolymers, and compounds derived from agricultural or industrial by
products.
- Controlled modification processes: Advanced techniques for controlling the
degree and distribution of organic modification are being developed to createorganobentonites with more precisely tailored properties. These include selective
edge modification, gradient modification, and multi-stage modification processes.
- Hybrid organic-inorganic modifiers: The combination of organic modifiers with
inorganic species such as metal oxides or silanes is being investigated to create
multifunctional organobentonites with enhanced thermal stability, catalytic
activity, or antimicrobial properties.
- Surface functionalization: Beyond traditional ion exchange modification,
researchers are exploring various surface functionalization techniques to introduce
specific functional groups onto the organobentonite surface, enabling new
applications and enhanced performance.
- Computational modeling: Advanced molecular modeling and simulation
techniques are being applied to better understand the structure-property
relationships in organobentonites and to predict the performance of new
formulations, accelerating the development process.
Environmentally Friendly Organobentonite Development
Environmental considerations are increasingly driving the development of new
organobentonite products:
- Bio-based modifiers: The use of modifiers derived from renewable resources, such
as plant oils, sugars, or agricultural waste, is gaining attention as a more
sustainable alternative to petroleum-based quaternary ammonium compounds
traditionally used in organobentonite production.
- Reduced environmental footprint: Manufacturers are working to reduce the
environmental impact of organobentonite production through process
optimization, energy efficiency improvements, and waste reduction measures.
- Biodegradable organobentonites: For applications where end-of-life
environmental impact is a concern, research is focusing on developing
organobentonites with biodegradable organic components that break down into
environmentally benign substances.
- Reduced VOC formulations: In response to increasingly stringent regulations on
volatile organic compounds (VOCs), new organobentonite products are being
developed that are compatible with low-VOC or VOC-free formulations in coatings
and other applications.
- Enhanced remediation capabilities: Advanced organobentonites with improved
selectivity and capacity for emerging contaminants, such as pharmaceuticals,personal care products, and microplastics, are being developed for environmental
remediation applications.
Multifunctional Composite Materials Research
The integration of organobentonite into advanced composite materials is an area of
active research:
- Nanocomposites: The development of polymer-organobentonite nanocomposites
with enhanced mechanical, thermal, and barrier properties continues to advance,
with applications in packaging, automotive components, and construction
materials.
- Smart materials: Researchers are exploring the incorporation of organobentonite
into responsive or “smart” materials that change their properties in response to
external stimuli such as temperature, pH, or electromagnetic fields.
- Multifunctional additives: Organobentonites that simultaneously provide
multiple functions, such as rheological control, reinforcement, flame retardancy,
and antimicrobial activity, are being developed to simplify formulations and
enhance overall performance.
- Hybrid aerogels and foams: The combination of organobentonite with various
polymer systems to create lightweight, high-performance aerogels and foams for
thermal insulation, filtration, and other applications is an emerging area of
research.
- Controlled release systems: The use of organobentonite as a carrier for active
ingredients in controlled release applications, such as agricultural chemicals,
pharmaceuticals, and fragrances, is being explored to enhance efficiency and
reduce environmental impact.
Application Domain Expansion
The unique properties of organobentonite are leading to its adoption in new application
domains:
- Advanced energy storage: Organobentonite is being investigated as a component
in electrode materials, separators, and electrolytes for batteries and
supercapacitors, where its barrier properties and thermal stability can enhance
safety and performance.
- Biomedical applications: Research into the use of organobentonite in drug
delivery systems, wound dressings, and tissue engineering scaffolds is expanding,leveraging its adsorption capabilities and potential for controlled release of
therapeutic agents.
- Food packaging: The barrier properties and potential antimicrobial functionality
of organobentonite make it interesting for advanced food packaging applications,
particularly for extending shelf life and improving safety.
- 3D printing formulations: The rheological properties of organobentonite are
being exploited in the development of specialized inks and feedstocks for various
3D printing technologies, enabling improved print quality and expanded material
options.
- Agricultural applications: From controlled-release fertilizers and pesticides to soil
amendments for contaminant immobilization, organobentonite is finding new
applications in sustainable agriculture.
Market Outlook and Analysis
The global market for organobentonite is expected to continue growing, driven by
several factors:
- Increasing demand for high-performance additives in industries such as coatings,
lubricants, and personal care products, particularly in emerging economies.
- Growing environmental concerns and regulations driving the adoption of more
sustainable and environmentally friendly materials.
- Expansion of application areas as new properties and functionalities of
organobentonite are discovered and developed.
- Technological advancements in production processes that improve efficiency and
reduce costs, making organobentonite more competitive with alternative
materials.
- Increasing research and development activities leading to new and improved
organobentonite products tailored for specific applications.
While challenges such as raw material availability, price volatility, and competition from
alternative technologies exist, the versatility and performance advantages of
organobentonite position it well for continued growth and development in the coming
years.Why Choose Our Organobentonite Products
When selecting an organobentonite supplier for your industrial needs, the quality,
consistency, and performance of the product are paramount. Our organobentonite
products stand out in the market due to our commitment to excellence in every aspect
of production, technical support, and customer service.
Product Quality and Consistency Assurance
Our organoclays bentonite products are manufactured under stringent quality control
standards to ensure consistent performance batch after batch. We understand that
consistency is crucial for your production processes, and we have implemented
comprehensive quality assurance measures to deliver products that meet your
specifications every time:
- We source only premium-grade bentonite with high montmorillonite content and
consistent mineralogical composition as the base material for our organobentonite
products.
- Our organic modification process is precisely controlled using advanced process
monitoring and control systems, ensuring uniform modification and consistent
product properties.
- Every batch undergoes rigorous testing for key parameters such as particle size
distribution, organic content, moisture level, and rheological performance before
release.
- We maintain detailed documentation and traceability for all production batches,
allowing us to quickly address any quality concerns and continuously improve our
processes.
- Our manufacturing facilities operate under ISO 9001 quality management systems,
with regular audits and certifications to ensure compliance with international
standards.
Technical Support and Customization Services
We recognize that each application has unique requirements, and our technical team is
dedicated to helping you select and optimize the right bentonite clay product for your
specific needs:
- Our experienced technical service team provides comprehensive support, from
initial product selection to troubleshooting and optimization of your formulations.• We offer customized product development services to create organobentonite
products tailored to your specific application requirements, whether you need
enhanced thermal stability, improved compatibility with particular systems, or
specialized rheological profiles.
- Our well-equipped application laboratories can conduct detailed performance
testing of organobentonite in your specific formulations, providing data-driven
recommendations for optimal results.
- We provide on-site technical support and training to help your team understand
the best practices for handling and incorporating organic clay into your
processes.
- Regular technical seminars and workshops keep you informed about the latest
developments in organobentonite technology and applications.
Sustainability Commitment
We are committed to sustainable practices in the production and application of our
organobentonite products:
- Our manufacturing processes are designed to minimize energy consumption, water
usage, and waste generation, reducing the environmental footprint of our
operations.
- We are actively developing and expanding our range of environmentally friendly
organic bentonite clay products, including those with bio-based modifiers and reduced
VOC requirements.
- Our research and development efforts focus on creating products that not only
enhance performance but also contribute to more sustainable end products and
processes for our customers.
- We provide transparent information about the environmental aspects of our
products, including their composition, potential environmental impact, and proper
disposal methods.
- We collaborate with customers, research institutions, and industry associations to
advance sustainable practices throughout the value chain.Success Case Studies
Our organo bentonite products have helped numerous customers across various
industries achieve significant improvements in their products and processes:
- A leading manufacturer of industrial coatings reduced formulation costs by 15%
while improving sag resistance and application properties by switching to our high
efficiency organobentonite product.
- An environmental remediation company achieved 30% higher removal efficiency
for organic contaminants using our specialized organo clays, significantly
reducing treatment time and costs for their clients.
- A major producer of lubricating greases extended the high-temperature
performance of their products by incorporating our thermally stable
organobentonite, opening new market opportunities in demanding applications.
- A foundry operation reduced emissions of volatile organic compounds by 40%
while improving casting surface quality by adopting our environmentally friendly
organobentonite binder system.
These success stories demonstrate the tangible benefits that our organophilic clays
products can bring to your operations, from cost savings and performance
improvements to environmental advantages and new market opportunities.
Contact Us for More Information
We are eager to discuss how our organobentonite products can benefit your specific
applications and help you overcome your technical challenges. Our team of experts is
ready to provide detailed information, product samples, and technical support to ensure
that you find the optimal solution for your needs.
Contact us today to learn more about our organoclay products and services.
Whether you have specific technical questions, need assistance with product selection,
or want to explore customization options, we are here to help you harness the full
potential of organobentonite technology for your business.
Email: [email protected]
Phone(Whatsapp): +86-13185071071
- Website:https://www.rheologymodifiers.com/
Let us be your partner in innovation and performance improvement through advanced